

After machining, the formed surface is checked by a template gauge. The irregular shapes can be convex, concave, or any other shape and are usually inspected using a template gauge. Sometimes, the contour will be ground on a single-point fly cutter. Formed cutters are ground to the shape of the contour of the workpiece and used on both vertical and horizontal milling machines. The form milling process allows for machining contours made up of curves and straight lines in a single cut. The angle cutter for the horizontal milling machine could be ground to a double angle for producing parts such as V-blocks. The last method is often used on Bridgeport-style vertical knee mills using a straight end mill and side-milling the workpiece. The angle milling operation can be accomplished in several different ways: with special form cutters mounted on a horizontal arbor, using end mills ground to the specific angle required, or by tipping the milling machine’s head to the proper angle. The cutting speed of a group of cutters is calculated from the cutter with the largest diameter.
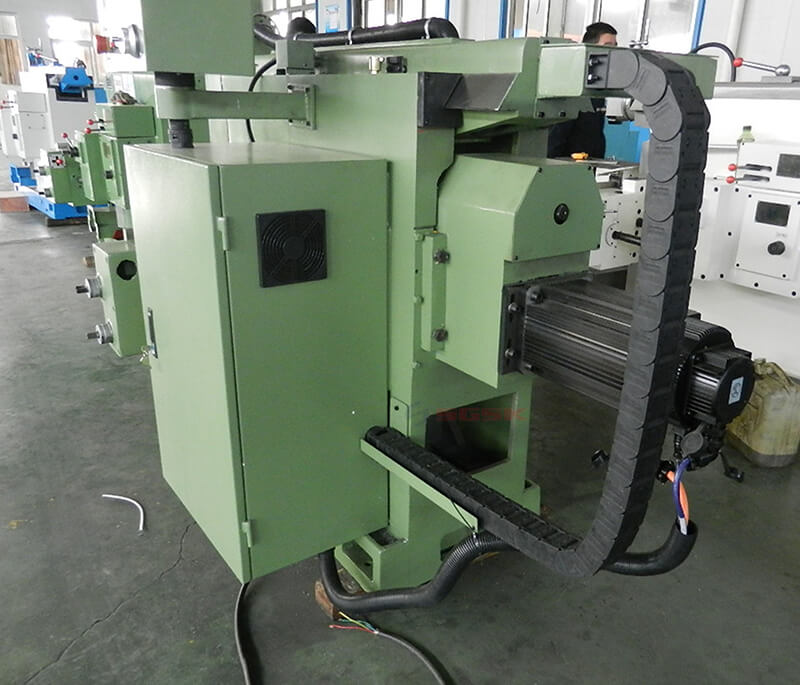
Gang milling saves machining time and is often used in repetitive work. The combination of cutters is determined by the requirements of the part and is virtually unlimited. Typically, milling cutters of different diameters, shapes, or widths are mounted on an arbor with spacing collars. The gang milling operation involves two or more milling cutters secured together on one arbor to machine several surfaces simultaneously. You can use the straddle milling operation to cut splines, squares, or a hexagon on the end of a round part. The cutters are kept apart by a spacing collar that’s the same dimension as the parallel sides so that they “straddle” the workpiece to produce the flat vertical surface. You accomplish this by mounting two side milling cutters on a horizontal milling machine on the same arbor. Straddle milling is used when you must have two or more parallel vertical surfaces machined in one cut. The side milling cutting tool is fastened to the horizontal arbor, and the table is raised to determine the depth of cut for milling slots or anything with a vertical wall.Īlthough the side milling cutter’s size, type, and diameter will depend on the machining, you should remember to use the smallest diameter cutter that will work properly and allow for sufficient clearance between the arbor support and workpiece or vise to keep the cutter’s flex to a minimum. If you are trying to produce a flat vertical surface in the workpiece, side milling is the option. After determining the correct feed and speed, the table is moved along the X-axis into the rotating cutter to remove material. Also referred to as slab milling or surface milling, the operation is done on a horizontal milling machine with the plain milling cutter adequately mounted on an arbor.Īn operator sets the depth of cut by cranking the vertical feed screw to raise the table. Plain milling is another common type of milling machine operation, producing a simple, flat, horizontal surface parallel to the axis of rotation of a plain milling cutter. It removes the material by rotating the facing tool in the counterclockwise direction as the table feeds the workpiece across the cutter.įace milling can be set up on either a vertical or a horizontal milling machine with the cutter mounted on a stub arbor. The facing operation is used only on flat surfaces perpendicular to the axes of the milling cutter. The teeth are on the outside and do most of the work, while the cutting edge on the face removes a tiny bit of material of stock left from the springing of the workpiece or cutter, providing a better surface finish. The workpiece’s dimensions determine the size and type of the face mill. The face milling operation is one of the simplest.
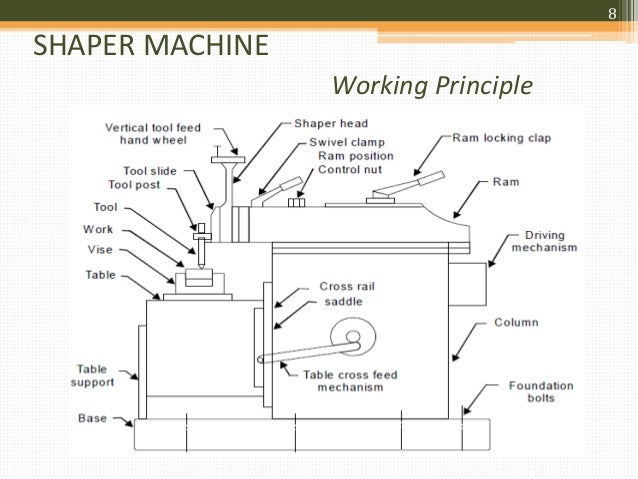
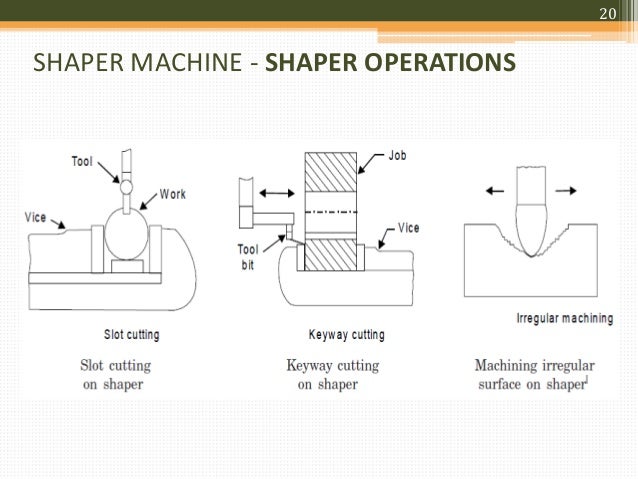
Although this is not an exhaustive list, it will cover most of them. The following are fifteen of the milling operations you can expect to perform on one of the many types of milling machines. One of the primary reasons for the popularity of the milling process is its ability to remove more material per cut than single-point cutting tools on a lathe machine, shaper, or planer. You’ll find a milling machine in nearly every machine shop and manufacturing facility, and the machinists working on them complete an array of cutting operations to produce finished parts. MX Electric Edge Finder and Z Axis Touch Plate.CNC 1440 Lathe Benchtop Turning Center Catalogue.– CNC SUPRA® Vertical Knee Mill 9 x 49 or 10 x 54.
